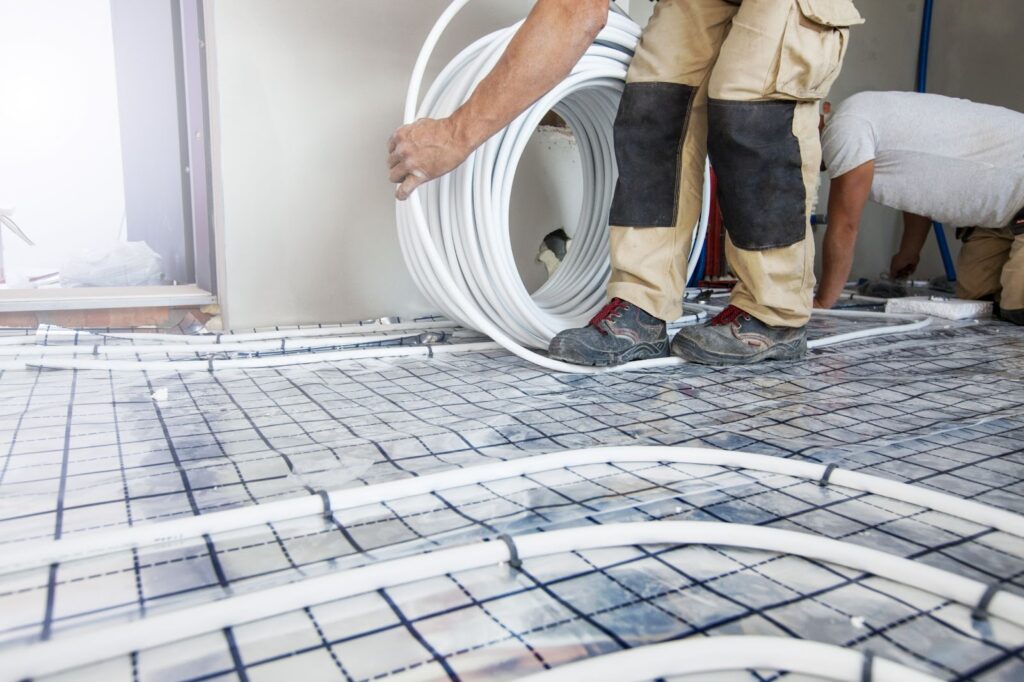
Underfloor heating systems provide even, efficient, and comfortable warmth for homes and businesses. Unlike traditional radiators, which heat the air, underfloor heating warms up solid objects that then emit heat over time.
Installing an underfloor heating system may seem daunting, but when properly planned out it can be a straightforward DIY project. This guide covers everything you need to know, from choosing the right type of system, floor coverings, insulation, and controls to step-by-step installation instructions.
Benefits of Underfloor Heating
- More comfortable – warms floors and lower areas of rooms
- No visible radiators or vents
- Even distribution of warmth
- Can be zones to independently control areas
- Works with renewable heating systems
- 25-40% more efficient than radiators
Drawbacks
- Higher initial cost
- Longer response time – floors take longer to heat up
- Not suitable for rooms below non-heated spaces
- Need larger heating boiler and pump
Types of Underfloor Heating Systems
There are two main types of underfloor heating to choose from:
Electric Underfloor Heating:
- Uses electric cables or mats
- Better suited to smaller spaces
- Easy DIY installation
- Can use renewable electricity
Hydronic (Wet) Underfloor Heating:
- Uses pipes of hot water from boiler
- Ideal for larger spaces
- Higher efficiency and controllability
- More complex installation
Within these types, you can choose loose wire cables, mats, or readymade panels.
Electric Underfloor Heating
Electric systems use heating cables or mats powered by electricity to warm the floor. They are easiest for DIY installation and well-suited to living areas, bathrooms, and conservatories less than 20 sq/m that need occasional heating.
Cables and mats sit underneath the floor surface, with sensor thermostats controlling the temperature. As electricity passes through the electric resistance wires, they gently heat up to around 40°C. This warmth gets emitted across the floor.
Electric systems respond faster than hydronic, making them handy for quickly heating bathrooms or living spaces as needed. They work as standalone systems with standard power outlets, requiring no boiler or plumbing.
Key components:
- Heating mats or loose cables
- Digital thermostat with floor sensor
- Monitoring device (recommended)
Pros
- Easy DIY installation
- Minimal floor thickness
- No plumbing or boiler is required
- Zonal control possible
- Fairly quick heat response
Cons
- Less energy efficient
- Not ideal for large spaces
- Can’t use renewable heat sources
Cost
£100 to £300 per sq/m installed
Hydronic Underfloor Heating
Hydronic or wet systems circulate hot water from a boiler through pipes laid on the floor to warm rooms. They offer the highest efficiency and are ideal for whole home heating, especially in new builds or renovations.
Pipes are embedded in the floor slab or underneath floor joists. Water from the gas boiler gets pumped to a manifold which then pushes it through the pipe loop at 35-50°C before returning back to the boiler.
Hydronic systems work best as whole-home solutions. They can use renewable heat sources and are very controllable with individual room thermostats. However they do require significant installation work, involving pipe routing and integrating into existing heating and plumbing systems.
Key components:
- PEX piping / Multilayer pipe
- Manifold station
- Room and sensor thermostats
- Mixing unit
- High-efficiency boiler
- Pump Group
Pros
- High efficiency – uses less energy
- Integrates renewable energy
- Even heat distribution
- Individual room control
- Almost invisible
Cons
- Complex installation
- Major renovation work
- Slow heat response time
Cost
£70 – £130 per sq/m installed
Read More: Are Home Improvements Tax Deductible?
Floor Coverings
Choosing appropriate flooring is important for performance and response times. The covering should conduct heat well but not insulate the floor excessively.
Best
- Stone and porcelain tiles
- Terracotta
- Slate
- Concrete slab
Good
- Engineered wood
- Vinyl
- Linoleum
- Cork
Unsuitable
- Deep pile carpets
- Wool carpet
- Underlay
Tile and stone allow fastest heat transfer. Engineered wood and harder floors work well. Soft carpeting is not suitable, though thinner types can be used with added care.
Insulation
Insulation plays a key role in underfloor heating performance. It greatly improves efficiency by minimizing downward heat loss into the subfloor. At least 70% of heat should go upwards.
Insulation acts as a reflective layer that keeps warmth in the room rather than wasting energy by heating lower floors and the ground underneath.
Insulation Tips
- Install below heating cables/pipes
- Use rigid insulation boards, not rolls
- Extruded polystyrene or foil-faced boards
- Compression strength >85 kPa
- Thermal resistance > 1 Tog
The level of insulation required depends on the floor build. But for ground floors aim for 100mm to 150mm of rigid extruded polystyrene. Suspended timber floors may need less insulation but still benefit from foil boards over the joists before laying cables or pipes.
Electric Underfloor Heating Installation
Installing electric underfloor heating consists of laying out the heating mats or cables onto insulation boards underneath the floor surface and embedding them in a self-leveling compound, tile adhesive, or grout layer.
Planning
- Calculate area and define installation zones
- Create a floor plan with required mats/cables
- Order extra spares for resilience
- Check floor depth and insulation needs
Tools Needed
- Tape measure
- Utility knife
- Cable cutters
- Clamps and pliers
- Masking tape
- Trowel and buckets
- Drill and screw gun
- Multimeter
- Hot glue gun
- Digital thermostat + sensors
- Monitoring device (optional)
Materials
- Heating mats or cables
- Thermal insulation boards
- Self-leveling compound
- Flexible tile adhesive
- Tile grout
- LVT click flooring
- Floor probes
- Trunk cables
- Conduit pipes
- Fixings
- jointing tape
Step-by-Step Installation
Follow these key steps to install electric underfloor heating:
- Prepare floor – Remove any existing coverings. Undercut walls. Clean and level subfloor.
- Lay insulation – Loose, rigid insulation boards with staggered joints. Consider additional edge insulation to limit heat loss. Seal gaps and tape joins.
- Mark sensor locations – Identify thermostat sensor placements, typically centered between wires in the warmest zones. These floor probes will control the heating.
- Lay out mats/cables – Unroll mats according to floor plan, maintaining 50mm spacing between wires. Trim to fit with sharp blades or wire cutters.
- Plan power feeds – Run trunk cables from main switch to areas under mats, leaving excess cable for termination. Use conduit for protection.
- Fix down cables – Secure power leads and mat joints with hot glue. Tape mats to subfloor, avoiding any pipes or obstructions in the floor.
- Take resistance reading – Use a multimeter to check resistance values to identify any damage to heating wires. Note for warranty purposes.
- Install floor probes – Position pre-wired sensor probes and leave excess cable to allow repositioning if needed after tiling.
- Cover cables – Apply self-leveling compound, flexible tile adhesive, or tile grout mix. For floating floors, use tile backer boards.
- Install floor – Tile floor as normal, taking care around sensor probes. Alternatively, install floating click laminate or vinyl planks according to manufacturer instructions.
- Connect electrics – Wire heating cables via isolator switch and fuse spur to main consumer unit observing all electrical safety regulations.
- Commission system – Set up Wi-Fi thermostat, configure floor probe, and test heating. Adjust temperature schedule and limits.
Hydronic Underfloor Heating Installation
Hydronic or wet underfloor systems require installation of pipe loops connected to a boiler and manifold to circulate hot water through the floor.
Design
- Create pipe layout plan
- Specify boiler, pump, and manifold
- Select-control system
- Size buffers and expansion tanks
Tools Needed
- Tape measure
- Utility knife
- Pipe cutters
- Deburring tool
- Crimping tool
- Spanner set
- Hammer drill
- Screw gun
- Handsaw
- Multimeter
- Digital manometer
- Thermostats
Materials
- Underfloor heating pipes
- Thermal insulation
- Manifold and fittings
- Thermo-actuators
- Floor brackets
- Pipe bending supports
- Ball valves
- Compression elbows
- Pipe insert fittings
- Pipe bending spring
- Fixings
- Commissioning fluid
Step-by-Step Installation
Major steps involved in installing hydronic underfloor heating:
- Insulate slab – For concrete subfloors lay 100-150mm rigid insulation before pouring concrete over pipes.
- Prepare floor – Secure battens to wooden subfloors. Lay foil-faced insulation between joists.
- Layout pipes – Route 16mm spaced parallel pipes in sweeping loops from manifold according to drawings. Fix with plastic U-clips ensuring pins do not damage pipes.
- Install manifold – Bracket manifold cabinets to wall with flow and return rails pointing upwards.
- Connect loops – Lay supply pipe from boiler into manifold. Use elbow fittings to connect pipe loops to relevant manifold supply channel.
- Install components – Mount electronic actuator valves onto manifold channels. Install pumps, check valves, drain valves, and fittings according to schematics.
- Lay screed – For concrete subfloors, cover pipes with 75mm screed using pipe embedding frames.
- Pressure test – Cap all floors and pressurize entire system to 6 bar over minimum of 30 minutes, inspecting for leaks and fixing as needed.
- Flush system – Connect temporary hose and flush entire system thoroughly. Drain and fill with heating fluid ready for commissioning.
- Commission – Adjust manifold valves. Bleed system. Set boiler and pump parameters. Check valve operations. Initialize and set room thermostats.
- Insulate screed – After curing insulation boards prior to applying floor finishes.
Controls and Accessories
Choosing the right controls and accessories ensures optimal comfort, efficiency and trouble-free operation.
Thermostats
Thermostats switch the heating on and off as needed to reach set temperatures based on readings from built-in or external sensor probes laid in the floor construction.
- Opt for Wi-Fi models allowing heating schedules via smartphone
- Zone larger areas with multiple thermostats
Monitoring
External control units continuously monitor electric heating mats and cables to detect any anomalies and prevent overheating risks. These monitor power, current leakage, insulation resistance, and floor temperature.
Manifold Actuators
Motorized actuators fitted to manifold stations open and close to regulate water flow to each loop. This enables zoning and room-by-room temperature controls when linked to thermostats.
Boiler Systems
Hydronic systems need connecting to high efficiency condensing boilers with sufficient output capacity, typically 24kW for a 4-bed home. Consider smart heating controls and buffered tanks allowing integration of solar thermal or heat pumps.
Commissioning
Always commission new underfloor heating systems properly to:
- Test all electrical connections
- Inspect water pipework
- Check flow rates
- Balance hydraulic circuits
- Bleed out air
- Set room thermostats
- Initiate self-learning modes
Thorough commissioning ensures systems operate safely and efficiently without any faults or leaks.
Maintenance Tips
- Use a soft brush attachment or mop when vacuuming floors
- Avoid dragging furniture or appliances
- Place area rugs away from obstructions
- Keep all floor probes and wiring accessible
- Check electric resistance values annually
- Inspect water pipes and joints before enclosing floors
- Top up water pressure
- Purge radiant systems annually
- Replace damaged heating elements
With proper care underfloor heating systems can last upwards of 50 years. But regular inspection and prompt repairs help maximize lifespan and efficiency.
Pros & Cons of Underfloor Heating
Pros | Cons |
No visible heat emitters | Slow heating response |
Comfortable even warmth | Require larger radiators |
25-40% more efficient | Increased installation cost |
Integrates green energy | Not suitable with some floors |
Independent zoning possible | Need insulation |
Conclusion
I hope this comprehensive guide gives you all the necessary information for considering underfloor heating systems. With good design and expert installation, these systems provide superior comfort and efficiency.
Although installation requires extensive floor preparation, the end results are worthwhile. Payback typically occurs within 5-15 years through energy savings.
If contemplating underfloor heating for new builds or renovations, consult technical specifications and ensure you engage certified plumbers and electricians for a safe and effective outcome that will keep homes comfortably warm for decades.