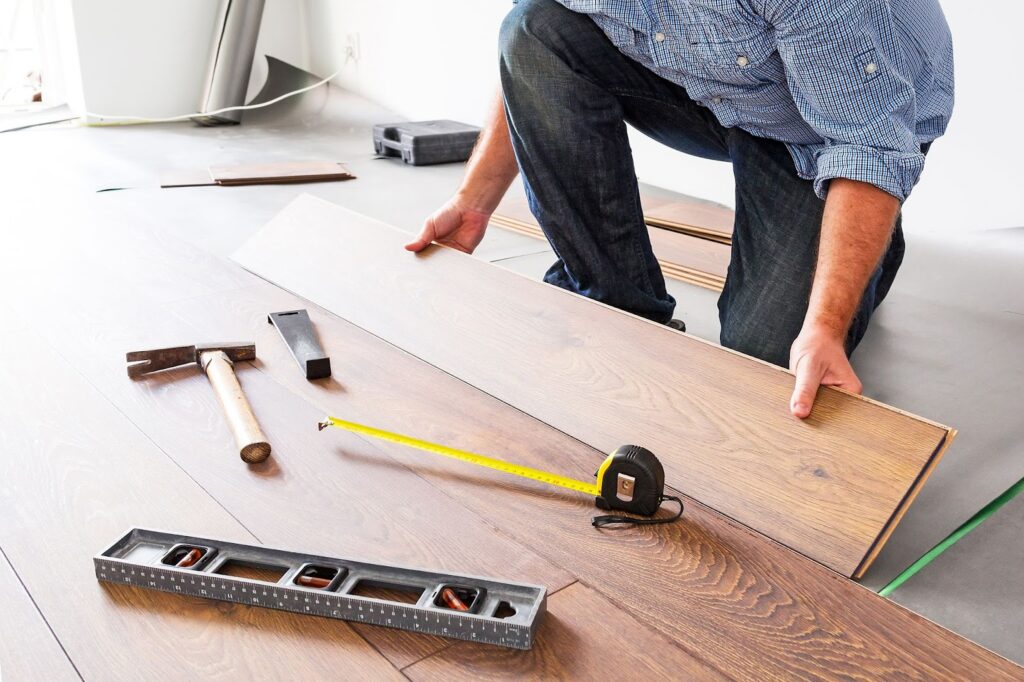
Installing a beautiful hardwood floor can greatly increase the value and aesthetics of your home. While hardwood is most commonly installed over wood subfloors, with proper preparation and technique, it can also be installed directly over concrete slabs. This brings the warmth and elegance of real wood floors even to basements, garages, and homes with concrete slab foundations.
In this DIY guide, we will cover everything you need to know for a successful hardwood floor installation over concrete, including:
- Preparing the concrete slab
- Choosing the right subflooring system
- Installing a vapor barrier
- Selecting the hardwood flooring
- Step-by-step installation guide
- Preventing moisture damage
- Troubleshooting common issues
Why Install Hardwood Over Concrete?
There are several great reasons to consider installing beautiful hardwood flooring over your concrete slab:
- Increased home value – Hardwood floors can increase your home’s resale value by 2-3x your installation cost. This makes it a worthwhile investment.
- Warmth and comfort – Hardwood imparts a warmth and softness that can’t be matched by cold, hard concrete alone. It’s also more comfortable to walk, stand, and work on for long periods.
- Beautiful aesthetics – Rich hardwood stain colors and wood grains bring life to any space and suit a variety of home décor styles.
- Acoustic benefits – Hardwood absorbs sound better than concrete and makes rooms feel quieter and more peaceful.
- Softer surface – Hardwood creates a softer landing for objects dropped on the floor, protecting them from damage.
As long as the slab is properly prepared first, installing hardwood is a durable and rewarding upgrade for any concrete foundation. Let’s go over how it’s done!
Preparing the Concrete Slab
Proper slab preparation is crucial for ensuring a long-lasting hardwood floor. Moisture and uneven surfaces will damage the floor over time. Concrete must be:
- Clean and free of contaminants
- Flat to 3/16 inches over 10 feet
- Dry year-round per flooring manufacturer’s requirements
Cleaning
The slab must be cleared of any materials or substances, like paint, wax, oil, adhesives, dust, sealer, curing compound, etc., that may prevent adhesion. Use a concrete degreaser and etch the surface with an acidic wash if necessary.
Leveling
Imperfections must be smoothed using a cement-based leveling compound. The surface should be flat within 3/16 inches over 10 feet. Test this using a 10-foot straightedge or screed. Any gaps below the straightedge exceeding 3/16 inches must be filled and leveled.
Moisture Testing
Concrete naturally holds significant moisture. This can damage the floor over time, so moisture testing is essential before installation. There are a few common ways to test moisture in concrete:
- Polyethylene sheet method – Tape down 2’ x 2’ plastic sheets in several areas and leave for 24 hours. Check underneath for condensation. Any condensation means the slab is too wet for hardwood installation.
- Calcium chloride test – Sealed test kits measure vapor emissions coming from the slab over 60-72 hours. Less than 3 lbs per 1,000 ft2 in 24 hours is suitable for hardwood.
- Relative humidity test – Sensors are placed in holes drilled into the concrete to measure interior humidity. Results below 75% indicate suitable concrete dryness levels for hardwood.
Moisture requirements can vary between hardwood manufacturers. Be sure to check what they specifically recommend. If high moisture is detected, consider installing a vapor barrier which we will cover further in the next section.
Other Considerations
- Is the slab heated? Heated slabs generally need to be kept below 85°F for proper hardwood installation.
- Are there any existing cracks? Small cracks should be filled and allowed to fully cure before installation. Large cracks may require an expansion joint in the floor above.
Once you’ve addressed cleaning, leveling, and moisture, you’re ready for subflooring!
Read More: How To Remove A Stripped Screw
Choosing the Right Subflooring System
Hardwood should never be installed directly over concrete. Gaps, moisture damage, and unstable surfaces will result. That’s where subflooring comes in — it spaces the wood away from the moisture and provides structural stability.
There are two main subfloor systems suitable for concrete slab installations:
1. Plywood with Screed Sleepers
This simple floating system uses 2×4 sleepers positioned 16 inches in center with plywood sheets screwed on top. Plywood thickness should equal the hardwood flooring thickness for a smooth installation.
Advantages:
- Cost-effective
- Allows easy access to under-floor utilities
- It can be unscrewed and removed easily for slab access
Disadvantages:
- Minimal insulation against slab moisture and temperature
- Prone to surface imperfections telegraphing through
2. Glue-Down Sleepers With Plywood
Glue-down sleepers are adhered directly to the slab in a mortar bed or construction adhesive to prevent movement. Plywood is then screw-fixed to the sleepers.
Advantages:
- Very stable surface for hardwood installation
- No surface imperfections are visible
- Insulates against moisture and temperature fluctuation
Disadvantages:
- Permanent installation makes under-slab access difficult
- More expensive installation
In general, glue-down sleepers create the most stable foundation and are recommended for best hardwood floor performance.
Additional Subflooring Tips:
- Use minimum 3/4” CDX plywood rated for flooring underlayment
- Stagger plywood sheet seams in a brickwork pattern
- Allow 1/8” gap at sheet edges and 1/2″ gap at walls for expansion
- Fasten plywood with 2” deck screws every 6 inches across joists/sleepers and every 12 inches along seams
With the right subfloor prepped, you’re ready for the next crucial layer — vapor barrier installation.
Installing a Vapor Barrier
Vapor barriers create a moisture-proof seal between the slab and floor to prevent moisture damage over time. Many experts consider it mandatory for reliable long-term performance.
There are a few common vapor barrier products:
- Plastic sheeting – Either 6mil polyethylene or laminated underlayment sheets work well. They’re affordable and easy to install but can tear and are difficult to repair once covered.
- Asphalt paper – Asphalt-saturated kraft paper offers excellent moisture resistance. However, overlap seams carefully as they can allow moisture through if compromised.
- Vapor barrier paint coatings – Special epoxy-based paints effectively seal porous concrete with a paint roller. This method is prone to application mistakes which lose effectiveness down the line.
For most DIY installations, thick polyethylene sheets are recommended as the most fool-proof and cost-effective vapor barrier.
Here are the installation steps:
- Sweep, then mop the floor to remove dust and debris. Let dry completely.
- Roll out sheets of 6mil+ polyethylene with 6” overlap at seams. Tape seams using moisture-proof tape.
- Roll plastic up walls 4-6 inches and secure to provide a humidity seal.
- Install sleepers directly over the plastic using adhesive or bottom-drilled screws with anchors. This prevents fastener holes in the moisture barrier.
- Construct subfloor over sleepers as normal. The plastic vapor barrier should now be fully sealed underneath.
With sublooring and vapor barrier complete, we’re now ready for beautiful hardwood installation!
Selecting Hardwood Flooring Materials
There are a few suitable hardwood flooring options for concrete subfloor installations:
Engineered Hardwood
Engineered hardwood is the #1 choice for concrete. Multiple wood veneers are layered over a water-resistant plywood core, making it highly stable on uneven surfaces while still providing a solid wood wear layer on top. It’s suitable for glue-down or floating installation.
Solid Hardwood
Solid 3/4″ thick oak planks can also be used but require a perfect slab and high attention to vapor sealing due to increased moisture sensitivity. Use premium grade boards that are more dimensionally stable.
WPC Vinyl Flooring
Luxury vinyl with an outer wood-plastic composite layer retains moisture resistance like vinyl but provides the look and feel of real wood. This is a great budget option for basements and garages but less value for primary living spaces.
Be sure to acclimate your flooring on-site for 1-2 weeks before installation. This allows the boards to adjust to your environmental conditions, preventing issues down the line. Now let’s get to the fun part —installing your beautiful new hardwood floor!
Step-by-Step Hardwood Installation
Follow these step-by-step instructions for proper installation over your prepared concrete slab:
1. Install Underlayment
Install 1/8” cork, foam, or felt underlayment per manufacturer instructions with plastic overlaps of 4-6”. This adds acoustic insulation, repairs small gaps, and prevents dust from coming up from below over time.
2. Lay Out Starter Boards
Select straight floorboards to create your starter row. Dry-fit them edge-to-edge with 1/4’’ spacers at all walls. Measure widthwise and rip final boards to size for a tight fit.
3. Glue Down Starter Boards
Apply urethane flooring adhesive using a 1/8” x 1/4” x 3/16” trowel at 45° angles across the length of the starters. Fit them back in place while wet, spacing evenly from walls.
4. Secure With Finishing Nails
Face nail installs your starter row using ring-shanked flooring nails driven at a 45° angle through the tongues at 8-10” intervals and 1-2” from board ends. Set nails slightly below surface.
5. Test Locking System
Connect your next row by engaging the boards’ locking system mechanisms. The tongue-and-groove should fit snugly but move into place without hammering. If very tight, lightly tap with a rubber mallet and pull bar.
6. Apply Adhesive & Blind Nail Remaining Rows
Continue blind/top nailing each following row using cleats angled through the tongue edge for a hidden appearance. Apply matching wood filler in all nail holes for a seamless finish.
Follow nailing and expansion gap guidelines from flooring manufacturers. Wipe away any adhesive seepage immediately using urethane adhesive remover and clean rags.
With those basic hardwood installation steps complete, your years of beautiful, reliable hardwood floors begin! Just be vigilant against moisture and swelling to ensure long-lasting durability and aesthetics.
Preventing Moisture Damage
While vapor barriers and engineered wood improve water resistance, additional precautions are still important for concrete hardwood floors:
Maintain indoor humidity between 30-50% year-round. Use dehumidifiers during wet seasons and humidifiers during excessively dry weather. This prevents wood swelling and shrinkage issues.
Don’t use water excessively on the floor beyond damp wiping. Control spillage and leaks immediately. Consider using interior-grade sealants occasionally over the years as added protection.
With proper installation and reasonable precautions, hardwood flooring over concrete offers great performance and can last decades before needing replacement. But if you do encounter issues down the line, here’s how to troubleshoot:
Troubleshooting Common Hardwood-Over-Concrete Issues
Cupping – Raised edges with sunken board middles. Cause is uneven moisture uptake across wood boards.
Solution: Check moisture barrier for damage and repair. Use dehumidifier and monitor conditions. Sand floor down and/or replace damaged boards.
Buckling – Raised floor humps and protruding edges. This happens with significant moisture build-up and wood expansion.
Solution: Identify and repair all moisture intrusion sources. Use fans, dehumidifiers, and AC to rapidly dry the slab. Re-install flooring if necessary. Consider solid hardwood limitations over concrete in extremely damp basements.
Rot & Decay – Soft, crumbly wood with dark water stains. Fungi and mold growth break down the floor over time.
Solution: Identify and resolve all moisture sources immediately. Dry out floor rapidly. Replace damaged boards and consider anti-microbial wood treatments to limit spread. Monitor conditions vigilantly afterward.
Loose Boards – Separated boards and unlocked click joints from wood shrinkage/swelling.
Solution: Remove sections and secure joints with adhesive and nails/screws. Consider refinishing entire installation for appearance consistency. Maintain indoor humidity in future.
Wear & Scratches – Surface damage from normal use over time.
Solution: Standard hardwood floor repair procedures apply like sanding, patching, staining, and refinishing to restore appearance and finish.
With attention and care, your installed hardwood floor should perform reliably for decades before needing replacement. Eventually, all floors require re-installation — when that time comes around to tackle this project again, use this same guide for exceptional results!
Conclusion
We’ve covered everything DIY homeowners need to successfully install beautiful, durable hardwood flooring over your concrete slab foundation. The keys are proper:
- Slab preparation
- Stable subflooring
- Moisture barriers
- Engineered flooring
- Expansion gaps
- Indoor humidity control
Follow the procedures described above, and your new floor will impress your guests’ socks off when they walk through the door! It can also add real resale value to make the work worthwhile as an upgrade investment over drab concrete.
As long as you maintain reasonable moisture precautions long-term and address any issues promptly if they arise, this hardwood flooring should retain its charm for many years before needing a refresh. Not to mention the acoustic and aesthetic boost it provides your space compared to cold hard concrete alone.
Hopefully, this gives you the confidence to tackle this project yourself. Hardwood floor installations may seem intimidating, but armed with the right techniques and knowledge, it can actually be a very satisfying do-it-yourself home improvement success story. Feel free to reference any part of this guide during your project!